Table of Contents
Table of Contents
Evaluating warehouse employee performance metrics is vital for optimizing efficiency and productivity in warehouse operations. This article delves into key metrics that provide insights into various aspects of employee performance, highlighting how they can be effectively measured and improved.
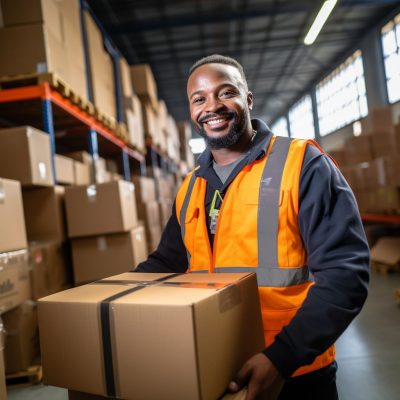
15 performance metrics for warehouse employees
Evaluating the performance of warehouse employees is crucial for ensuring operational efficiency and effectiveness. By tracking specific metrics, managers can gain insights into various aspects of warehouse operations, from accuracy and productivity to safety and customer satisfaction.Â
Here’s a list of 15 key performance metrics that can help in assessing and improving the performance of warehouse employees:
- Picking accuracy (PA)
- Order fulfillment rate (OFR)
- Safety compliance (SC)
- Productivity per hour (PPH)
- Labor cost per unit (LCPU)
- Inventory count accuracy (ICA)
- Cycle time (CT)
- Loading and unloading efficiency (LUE)
- Attendance and punctuality (AP)
- Quality control compliance (QCC)
- Equipment handling proficiency (EHP)
- Return processing time (RPT)
- Space utilization efficiency (SUE)
- Customer satisfaction metrics (CSM)
- Continuous improvement initiatives (CII)
These metrics provide a comprehensive view of employee performance, covering aspects like efficiency, accuracy, safety, and overall effectiveness. Regular monitoring and analysis of these metrics enable warehouse managers to identify areas needing improvement, recognize high performers, and make informed decisions to enhance the overall productivity and safety of warehouse operations.
1. Picking accuracy (PA)
Picking accuracy formula: (Total Correct Picks/Total Picks) x 100
Picking accuracy measures the percentage of orders picked without errors. It’s tracked by comparing the actual items picked against the order list. Higher values are better as they indicate fewer picking mistakes. Tracking this metric is crucial for minimizing errors in order fulfillment. A low picking accuracy can lead to increased returns and customer dissatisfaction.
How to improve picking accuracy:
- Implement barcode scanning to ensure correct item picking.
- Provide regular training to staff on accurate picking methods.
- Utilize pick-to-light systems for error reduction.
- Conduct frequent audits to identify and correct picking errors.
- Encourage a double-check or peer-review system.
- Optimize warehouse layout for easier item location.
- Implement incentive programs for accurate picking.
2. Order fulfillment rate (OFR)
Order fulfillment rate formula: (Total Orders Fulfilled on Time/Total Orders) x 100
Order fulfillment rate assesses the proportion of orders fulfilled on time. It’s calculated by dividing the number of orders shipped on time by the total number of orders. Higher rates are better, indicating effective and timely order processing. Tracking this metric helps in evaluating the efficiency of the order processing system. Poor values might indicate issues in inventory management or processing delays.
How to improve order fulfillment rate:
- Optimize inventory management to avoid stockouts.
- Streamline the order processing system.
- Implement an efficient warehouse management system (WMS).
- Enhance communication and coordination among staff.
- Automate certain steps in the fulfillment process.
- Regularly review and adjust fulfillment strategies.
- Monitor supplier performance to ensure timely restocking.
3. Safety compliance (SC)
Safety compliance formula: (Number of Adherences to Safety Procedures/Total Safety Checks) x 100
Safety compliance tracks adherence to warehouse safety protocols. It’s measured by observing and recording adherence to safety standards during operations. Higher compliance rates are desirable, indicating a safer working environment. Monitoring this metric is essential for reducing workplace accidents and ensuring employee well-being. Low compliance can lead to increased accidents and potential legal issues.
How to improve safety compliance:
- Conduct regular safety training and drills.
- Clearly communicate safety guidelines to all employees.
- Enforce strict adherence to safety protocols.
- Regularly inspect and maintain equipment and facilities.
- Encourage employee feedback on safety concerns.
- Implement visual safety aids and signage.
- Reward compliance and improvement in safety practices.
- Use your warehouse security camera system to perform more safety audits.
4. Productivity per hour (PPH)
Productivity per hour formula: Total Units Processed/Total Hours Worked
Productivity per hour evaluates the amount of work, like the number of orders processed or units handled, completed per hour. Higher values indicate greater efficiency. This metric is crucial for understanding workforce efficiency and optimizing labor utilization. Low productivity per hour could signal inefficiencies, insufficient training, or inadequate resource allocation.
How to improve productivity per hour:
- Implement lean management principles to eliminate waste.
- Use technology to automate repetitive tasks.
- Provide training to enhance worker skills and efficiency.
- Optimize the warehouse layout for smoother operations.
- Set clear goals and expectations for employees.
- Monitor and analyze productivity data to identify bottlenecks.
- Encourage regular breaks to maintain employee focus and energy.
5. Labor cost per unit (LCPU)
Labor cost per unit formula: Total Labor Cost/Total Units Handled
Labor cost per unit calculates the cost of labor for each unit handled in the warehouse. It’s determined by dividing the total labor cost by the total number of units processed. Lower values are preferable, indicating more cost-effective labor utilization. This metric helps in assessing labor efficiency and financial performance. High labor costs per unit can signal inefficiencies or overstaffing.
How to improve labor cost per unit:
- Improve labor scheduling to match workflow demands.
- Enhance process efficiency to reduce labor hours per task.
- Automate tasks where possible to reduce manual labor.
- Provide training to increase worker speed and efficiency.
- Monitor and optimize overtime use.
- Implement cross-training to utilize labor more flexibly.
- Look out for late starts, long breaks, and other forms of time theft.
- Analyze workflows to identify and eliminate inefficiencies.
6. Inventory count accuracy (ICA)
Inventory count accuracy formula: (Correct Inventory Counts/Total Inventory Counts) x 100
Inventory count accuracy evaluates how accurately employees count inventory. It’s calculated by comparing the results of physical counts to system records. Higher accuracy rates are better, ensuring reliable stock data for order fulfillment and planning. Poor inventory count accuracy can lead to stock discrepancies, affecting order processing and inventory management.
How to improve inventory count accuracy:
- Conduct regular and systematic inventory audits.
- Use barcode or RFID systems for accurate tracking.
- Train employees thoroughly in inventory counting procedures.
- Implement cycle counting to manage inventory accuracy continuously.
- Utilize inventory management software for better tracking.
- Encourage a culture of attention to detail among staff.
- Review and refine inventory counting processes regularly.
7. Cycle time (CT)
Cycle time formula: Total Time Taken for Tasks/Total Number of Tasks
Cycle time is the duration taken to complete specific tasks in the warehouse, such as picking or packing an order. Shorter cycle times indicate higher efficiency. It’s measured by timing how long tasks take to complete. Lower cycle times are preferable, reflecting faster operations. High cycle times might indicate process bottlenecks or inefficiencies.
How to improve cycle time:
- Streamline workflows to eliminate unnecessary steps.
- Implement efficient layout and organization of the warehouse.
- Use automation to speed up repetitive tasks.
- Provide training to enhance employee speed and efficiency.
- Use time-tracking tools to identify and address delays.
- Encourage continuous improvement and feedback from employees.
- Regularly review and update processes and equipment.
8. Loading and unloading efficiency (LUE)
Loading and unloading efficiency formula: (Total Units Loaded/Unloaded/Total Time for Loading/Unloading)
Loading and unloading efficiency measures the speed and accuracy with which employees load and unload goods. It’s calculated by dividing the total units loaded/unloaded by the total time taken for these activities. Higher efficiency is better, indicating quicker turnaround times and reduced bottlenecks. Low efficiency can lead to delays in shipping and receiving.
How to improve loading and unloading efficiency:
- Implement organized and standardized loading procedures.
- Use appropriate and well-maintained equipment.
- Train staff on efficient loading and unloading techniques.
- Schedule loading/unloading to avoid peak times and congestion.
- Optimize warehouse layout for easier access to goods.
- Regularly maintain and service loading equipment.
- Implement teamwork strategies to streamline the process.
9. Attendance and punctuality (AP)
Attendance and punctuality formula: (Total Scheduled Hours/Total Hours Attended) x 100
Attendance and punctuality monitor employees’ adherence to scheduled work hours. It’s calculated by comparing actual hours worked to scheduled hours. Higher rates indicate better adherence to schedules, essential for maintaining consistent workflow. Poor attendance and punctuality can disrupt operations and reduce overall productivity.
How to improve attendance and punctuality:
- Implement flexible scheduling to accommodate employee needs.
- Set clear expectations and consequences for tardiness and absences.
- Offer incentives for consistent attendance and punctuality.
- Use time-tracking software for accurate monitoring.
- Address any underlying issues causing poor attendance.
- Provide support for transportation or childcare if necessary.
- Foster a positive work environment to encourage employee commitment.
10. Quality control compliance (QCC)
Quality control compliance formula: (Number of Products Meeting Quality Standards/Total Products Inspected) x 100
Quality control compliance assesses adherence to quality standards in handling and processing goods. It’s measured by inspecting products and comparing them to quality benchmarks. Higher compliance rates are better, indicating fewer defects and higher quality outputs. Tracking this metric is important for maintaining product quality and customer satisfaction. Low compliance rates can lead to increased returns and damage to the company’s reputation.
How to improve quality control compliance:
- Provide comprehensive training on quality standards.
- Implement regular quality inspections and audits.
- Use technology for precise measurement and error detection.
- Encourage a culture of quality and attention to detail.
- Continuously review and update quality standards.
- Foster open communication about quality issues and improvements.
- Recognize and reward adherence to quality standards.
11. Equipment handling proficiency (EHP)
Equipment handling proficiency formula: (Number of Successful Equipment Operations/Total Equipment Operations) x 100
Equipment handling proficiency evaluates skill in using warehouse equipment like forklifts. It’s calculated by observing and recording successful operations versus total operations. Higher proficiency rates are desirable, indicating safe and effective equipment use. Monitoring this metric is crucial for ensuring operational efficiency and safety. Poor proficiency can lead to increased accidents and equipment damage.
How to improve equipment handling proficiency:
- Provide regular and comprehensive equipment training.
- Implement a certification process for equipment operators.
- Conduct routine equipment checks and maintenance.
- Create a mentorship program for less experienced operators.
- Encourage practice and hands-on experience.
- Monitor and address equipment-related incidents promptly.
- Update or upgrade equipment to newer, more efficient models.
Â
12. Return processing time (RPT)
Return processing time formula: Total Time Taken for Return Processing/Total Number of Returns
Return processing time measures the efficiency in handling returns. It’s calculated by dividing the total time taken for return processing by the number of returns. Lower times are better, indicating quicker and more efficient handling of returns. High return processing times can lead to customer dissatisfaction and increased costs.
How to improve return processing time:
- Streamline the return process with clear procedures.
- Implement dedicated staff or teams for return processing.
- Use technology to track and manage returns efficiently.
- Provide training on efficient handling of returns.
- Continuously review and adjust the return process.
- Encourage feedback from employees on process improvements.
- Automate data entry and processing steps where possible.
13. Space utilization efficiency (SUE)
Space utilization efficiency formula: Used Space/Total Available Space×100
Space Utilization Efficiency (SUE) assesses how effectively warehouse space is used. It compares the occupied space against the total available space. Higher values indicate better utilization. Efficient space usage maximizes storage, reduces clutter, and enhances workflow. Low SUE may signal underused space, inefficient layout, or overstocking.
How to improve space utilization efficiency:
- Reevaluate and optimize the warehouse layout regularly.
- Utilize vertical space for storage to free up floor space.
- Implement just-in-time inventory to minimize overstocking.
- Invest in compact, space-efficient storage solutions.
- Conduct regular inventory audits to identify and reduce excess stock.
- Implement a Warehouse Management System (WMS) for better space management.
- Train staff in efficient space utilization techniques.
14. Customer satisfaction metrics (CSM)
Customer satisfaction metrics formula: Variable (based on specific metrics like customer satisfaction score or net promoter score)
Customer satisfaction metrics (CSM) gauge customer satisfaction with warehouse services, focusing on order accuracy and delivery times. These metrics are derived from customer feedback and surveys. Higher scores denote greater customer satisfaction. Tracking CSM is crucial for understanding customer needs and maintaining a positive brand reputation. Poor scores may indicate issues in order fulfillment or product quality.
How to improve customer satisfaction metrics:
- Enhance order accuracy through rigorous checking.
- Streamline processes for faster delivery.
- Provide exceptional customer service for inquiries and concerns.
- Regularly seek and act upon customer feedback.
- Offer customization options and flexible delivery.
- Train staff in customer service and efficient order processing.
- Employ technology for real-time monitoring and process optimization.
15. Continuous improvement initiatives (CII)
Continuous improvement initiatives formula: Not applicable (qualitative metric)
Continuous Improvement Initiatives (CII) measure employee involvement in enhancing warehouse operations. This qualitative metric evaluates the number and effectiveness of improvement projects. Active participation in CII indicates a commitment to operational excellence. Limited involvement might suggest a lack of innovation or adaptability.
How to improve continuous improvement initiatives:
- Foster a culture that values employee feedback and suggestions.
- Create formal channels for submitting and reviewing improvement ideas.
- Recognize and reward contributions to process enhancements.
- Offer training in problem-solving and continuous improvement methodologies.
- Facilitate collaboration across various departments for diverse insights.
- Conduct regular process reviews to identify potential improvements.
- Utilize analytical tools to pinpoint areas for efficiency gains.
Use Solink to monitor warehouse employee performance
Tracking the performance of warehouse employees is essential for maintaining an efficient and productive operation. Solink offers a powerful solution for this purpose. By integrating cloud video security with analytics, Solink provides real-time insights into warehouse activities. This technology enables managers to monitor key performance metrics, ensuring that operations run smoothly and efficiently.Â
With Solink, businesses can enhance safety, improve employee productivity, and ultimately achieve higher customer satisfaction, making it an invaluable tool in the modern warehouse environment.
To see how Solink can help boost warehouse employee performance, sign up for a demo today.