Inventory shrinkage refers to all the products a business loses due to theft, fraud, damage, or wastage. Reducing these losses is crucial for any business.
Shrink is on the rise. The 2020 National Retail Security Survey reports an average retail shrink of 1.62% with 18.2% of all retailers experiencing inventory shrinkage in excess of 3%.
Much of this increased shrinkage is directly attributable to the rise of organized retail crime (ORC), with over 60% of loss prevention professionals considering ORC a higher priority than in previous years.
Solink provides the tools you need to reduce shrinkage today. In this article we’ll discuss how by connecting the data from your video security system, POS, and more, you will be in an overall better position to fight against shrink. Solink shows you how you can reduce shrinkage easily.
To see how Solink can help you find and eliminate shrink, sign up for a demo today right here.
What is inventory shrinkage?
As mentioned above, inventory shrinkage occurs when there’s a discrepancy between the expected inventory value, based on order and sales data, and the actual inventory value.
Many different things contribute to inventory shrinkage. Here are the main ones:
- Theft and fraud
- Accounting errors
- Wastage
- Damaged merchandise
Shrinkage can either be normal (planned) or abnormal (due to errors or dishonesty). It is also found across every industry in need of security.
Easy to understand inventory shrinkage examples
Here are some examples of inventory shrinkage:
Retail shrinkage example
A shipment arrives including 60 t-shirts. In the first three weeks, your point of sale (POS) shows that you have sold 20 of them. However, a count of the merchandise reveals there are only 36 t-shirts left on the shelf. You’ve experienced 4 t-shirts of inventory shrinkage.
Restaurant shrinkage example
Normal shrinkage: A restaurant orders whole slabs of beef. They need to trim some of the fat before selling the individual portions as steaks. The trimmed fat represents normal inventory shrinkage.
Abnormal shrinkage: A restaurant orders boxes of chicken breasts to cut into chicken fingers. Due to poor inventory management, the newer product is placed in front of the older product in the fridge. The older product is not used before it goes bad. This is abnormal shrinkage due to inventory management errors.
Explaining inventory shrinkage in different industries
Shrinkage occurs across all industries and at every point in the value chain. Sometimes it is normal shrinkage, which is planned and can only be minimized. Other times it is abnormal, and the goal should be to eliminate it.
Retail shrinkage
Retail environments are hard hit by shrinkage. While you might not think there is normal retail shrinkage, there definitely is. Just like meat and vegetables, fashion has a “best before date,” and goods that do not sell before styles change require heavy discounts to entice customers.
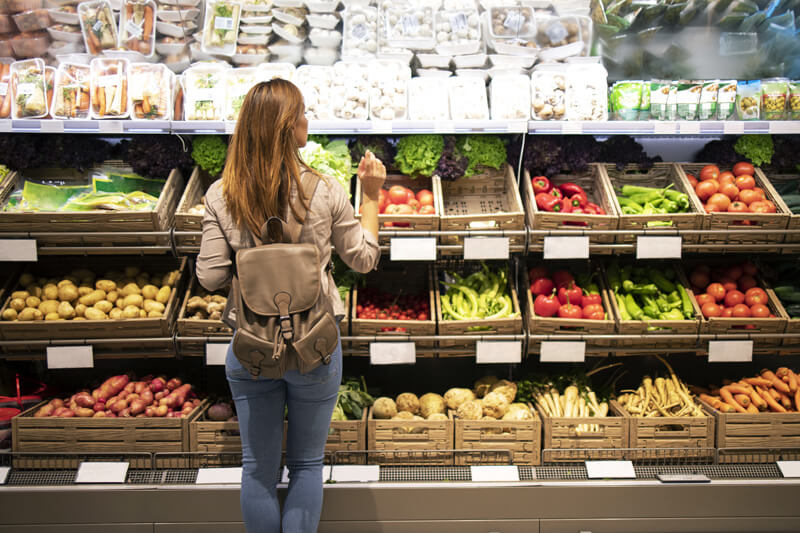
However, in the retail industry, abnormal shrinkage is far more common. This is why it is important to have a loss prevention system in place. Internal theft, shoplifting, damaged products, and incorrect ordering all negatively impact the inventory shrinkage rate of retail stores.
Retail shrinkage is a significant financial burden, exceeding $100 billion in losses in 2022. This trend of increasing losses is capturing the attention of retail executives and investors alike. While customer theft and shoplifting are common sources, shrinkage encompasses losses across the entire value chain, including damage and errors, from multiple trusted stakeholders such as employees and third parties. Addressing this requires a comprehensive, data-driven approach to understand and mitigate the various sources of shrink (EY US).
Warehouse and logistics shrinkage
Warehouses, logistics centers, and shipping companies represent major sources of shrink in most value chains. Products are moved around large facilities, stacked, and moved again, often using forklifts or other heavy machinery.
Items are often damaged, and the overlapping areas of control make theft possible as well. Solink provides specific tools to help these industries because the risk of shrinkage is so high. In addition, the value of inventory is often much greater than any individual store or restaurant, so any reduction in the inventory shrinkage rate will represent a major return on investment (ROI).
Manufacturing shrinkage
Regardless of what is being manufactured, there will always be some materials lost. Here are some examples of normal and abnormal shrinkage in two very different manufacturing environments: a car parts factory and a winery.
The stamping pattern in the car parts factory uses 98% of the steel sheet. The other 2%, less any value recoverable from recycling, is normal shrinkage. The same factory experiences a defect that stains one side of the stamped parts, which cannot be sold. This is abnormal shrinkage.
A winery produces 300 liters of wine. They bottle their wine in 750 milliliter bottles. During the bottling process, they only fill 398 bottles instead of the expected 400. This is normal shrinkage due to spillage. Then, when loading the truck with cases to send to the warehouse, an employee drops a case, shattering 12 bottles. This accident represents abnormal shrinkage.
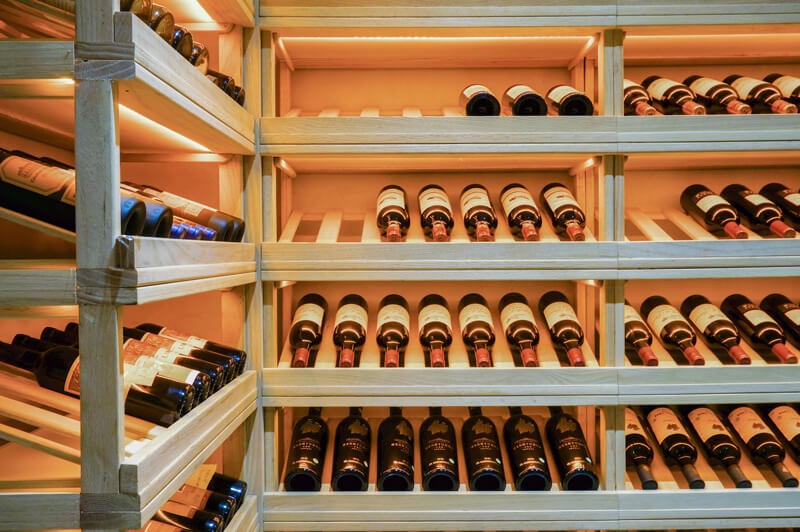
Restaurant and hospitality shrinkage
Restaurants and hotels experience both normal and abnormal shrinkage. There will always be a difference in the amount of food being ordered and what is served to customers. However, there are situations which could lead to especially high shrinkage:
- Kitchen staff are regularly burning food or errors at the POS are leading to incorrect dishes being prepared.
- Kitchen staff are improperly trimming meat and vegetables, resulting in edible food being discarded.
- Poor inventory management is leading to stock expiring before it is served to customers.
- Low quality inventory from suppliers is leading to excess wastage.
- Bartenders and servers are giving away drinks and food to their friends and family (this is just one form of employee theft that you should keep an eye on).
- Poor or deceitful food preparation planning at quick service restaurants (QSRs) leads to excess wastage at the end of night.
Breaking down 7 key causes of inventory shrinkage (with examples)
There are many sources of inventory shrinkage. Some of them can’t be avoided. Others can be avoided and should not be accepted as simply the cost of doing business. Here are 7 causes of shrinkage that you should try to eliminate:
- Shoplifting
- Employee theft
- Damage
- Wastage
- Administrative errors
- Supplier fraud
- Unknown
Shoplifting
Shoplifting is rising, and the forms of shoplifting have changed drastically over the last decade. Now, organized retail crime (ORC) is a far bigger source of external theft than ever before. In ORC, several criminals coordinate their activities to steal even more merchandise. These ORC attacks are often backed by large criminal organizations. Note that ORC is not limited to shoplifting, but also includes return fraud, credit card fraud, intensity theft, and counterfeiting of currency, receipts, and price tags.
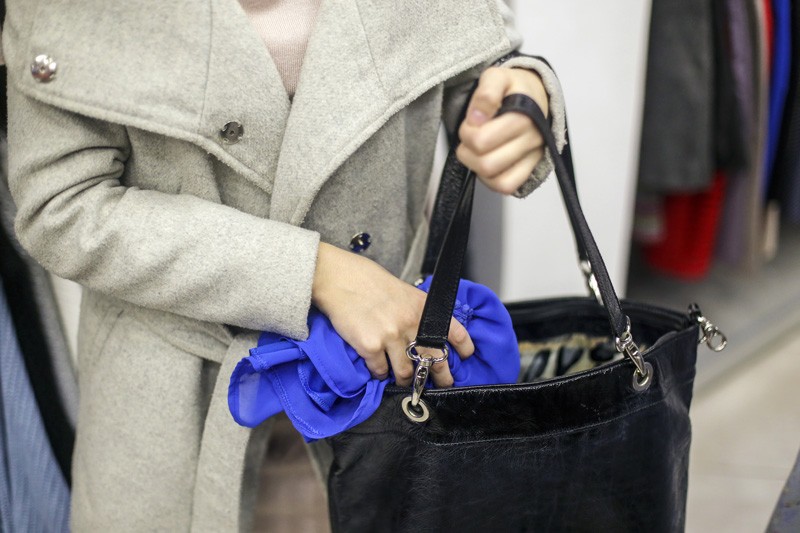
We dedicate an entire article to teach you how to spot a shoplifter because this source of inventory shrinkage is only growing in importance.
Shoplifting remains one of the most straightforward yet challenging forms of shrinkage for retailers to manage, requiring effective security measures and staff vigilance. An example of shoplifting as a form of inventory shrinkage could involve a customer discreetly placing a small, high-value item—like a piece of jewelry or an electronic device—into their pocket or bag without paying. This act not only reduces the physical stock available for sale but also impacts the store’s revenue and profit margins.
Employee theft
Employee theft is a major source of inventory shrinkage. In fact, the 2020 National Retail Security Survey states that a single dishonest employee costs a company on average over $1,100. That’s compared to only $800 per shoplifter.
Employee theft as a form of inventory shrinkage might involve a scenario where a staff member uses their access to the stockroom to unlawfully take merchandise, like clothing or electronic gadgets. This theft not only depletes the inventory but also affects the financial health of the business, as it directly leads to lost sales opportunities and additional restocking costs. Such situations highlight the need for stringent inventory control measures and employee screening processes to mitigate insider theft.
Given the cost of complacency, you should be doing everything in your power to prevent employee theft.
Damage
Maintaining a clean and organized store front and back room can reduce the likelihood of merchandise being damaged.
Damage as a form of inventory shrinkage can occur when items are mishandled during shipping, stocking, or by customers. For example, electronic devices might be dropped, resulting in internal damage that renders them unsellable. This not only reduces available inventory but also incurs additional costs for disposal or markdowns, directly impacting the store’s profitability. Effective training on handling procedures and proper packaging can help mitigate such losses.
Solink allows you to video audit stores for regulatory and company policy compliance from head office. Being able to see in minutes whether the back rooms of all your locations are neat and tidy will help reduce shrinkage due to damaged products.
Wastage
Poor employee training and lack of adherence to company policy will increase the amount of items that need to be thrown out.
Wastage as a form of inventory shrinkage typically involves perishable goods like food that spoil before being sold. For instance, in a grocery store, fresh produce that isn’t sold within its shelf life and must be discarded contributes to wastage. This results in direct losses for the store, as resources spent on purchasing, transporting, and storing these goods do not translate into sales. Efficient inventory management and timely promotions can help reduce such wastage.
Did you know that your business security camera system can also help with employee training? Solink helps you uncover what is happening in your business by providing you with actionable data when you need it.
To see where Solink can reduce your inventory shrinkage, sign up for a demo today.
Administrative errors
Accounting and administrative errors happen. The best way to minimize the cost of these errors is to back up your inventory management system data with manual effort. Indeed, it is impossible to know how much inventory shrinkage has occurred if you are not manually auditing your inventory regularly.
Manual inventory counts can also reduce the risk of accidental orders or unnecessarily large purchases that may lead to excess wastage.
Administrative errors as a form of inventory shrinkage can include mistakes like mispricing items, incorrect stock data entry, or errors in inventory counting. For example, if an employee inaccurately records the receipt of fewer units of a product than were actually delivered, it can cause discrepancies in inventory records, leading to misinformed restocking decisions and potential sales losses. Proper training and the use of automated systems can help reduce the incidence of such errors.
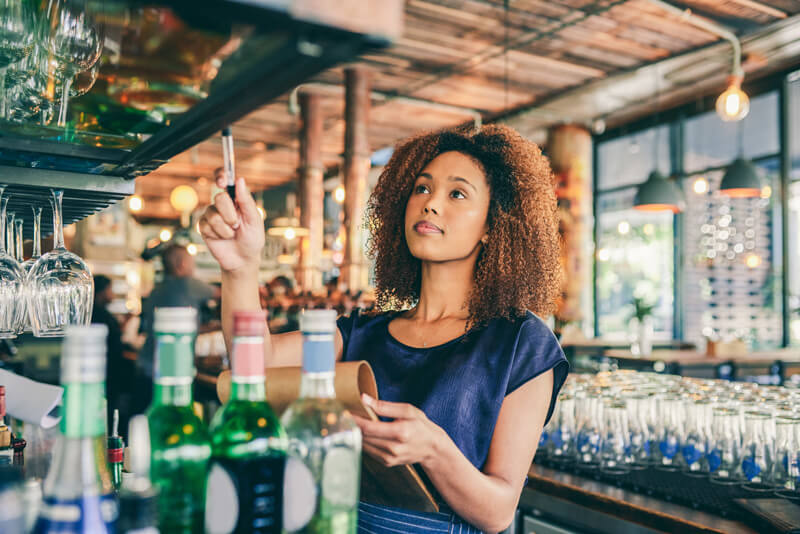
Supplier fraud
Theft can occur between when merchandise exits the warehouse and enters the store. It is important to instruct employees to always check their manifests and only sign off on deliveries when everything on the manifest has been delivered.
Supplier fraud as a form of inventory shrinkage occurs when vendors manipulate transactions or deliver substandard goods that don’t meet the order’s specifications or quantities. An example is a supplier invoicing for a higher quantity of items than was actually delivered, or providing goods that are of inferior quality, leading to unsellable stock. These actions cause discrepancies in inventory levels and financial losses. Rigorous vetting of suppliers and regular auditing of goods received can help prevent this type of shrinkage.
Unknown causes
Some inventory shrinkage is caused by unknown sources. This is troubling because it represents missing information. You cannot reduce shrinkage if you don’t know the source.
Solink’s integrated VSaaS solution helps remove this uncertainty by connecting all of your data sources. The first step in eliminating inventory shrinkage is to find the sources. Solink helps you do this by giving you video footage of everything happening in your business without the need to manually search through the security video.
Easy ways to prevent inventory shrinkage
Inventory shrink is hurting your business. Thankfully, there are ways to reduce inventory shrink. Considering how much inventory shrink can cost you, the ROI of a solution that helps eliminate it is significant.
Invest in a business security system
You probably have security cameras in your store, but do you have a complete business security camera system? Cameras are only one part of a complete security system. You also need a video analytics system that integrates with your security system, POS, and more to provide insights into your business.
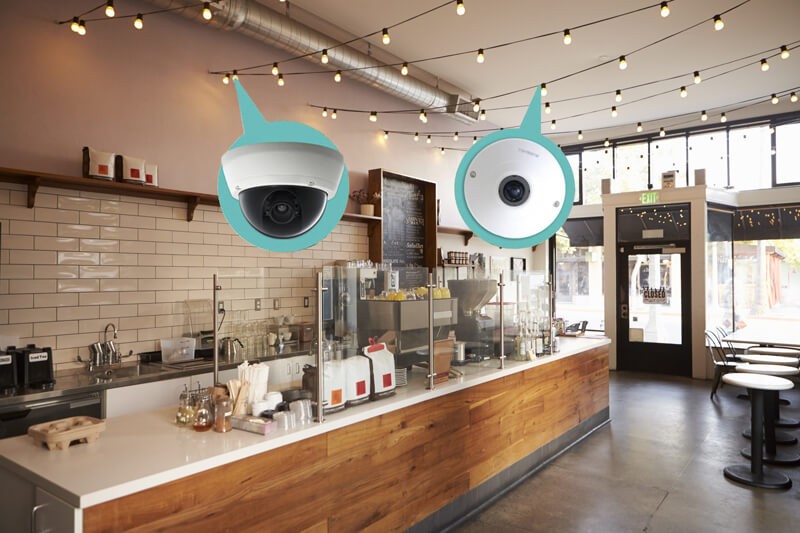
Solink is this solution. Remember, inventory shrinkage can be caused by employee training deficits and not just theft. You might not think of your security cameras as an employee training tool, but it has a direct impact on employee training. In fact, as a great example Negril considers finding employee training opportunities one of the biggest value adds of Solink’s platform.
Use an electronic article security system
An electronic article security (EAS) system can help you follow inventory throughout your store and make sure that it only leaves through a legitimate purchase. An EAS system is a great way to keep track of all of your inventory, but especially the smaller and higher-value items.
For instance, a retail clothing store can attach security tags to garments. If someone tries to leave the store without paying for these tagged items, the EAS system’s gates at the store exit will detect the tags and sound an alarm. This not only discourages shoplifting but also alerts staff to potential thefts, allowing for quick intervention.
Count inventory often
How often do you count your entire inventory? Implementing regular counts of your inventory can help you track down sources of shrinkage. Consider increasing the frequency of your counts, for example from annually to quarterly, to get a better understanding of your inventory shrinkage.
Surprise audits
While full inventory counts are mandatory, employees might time their thefts to occur shortly after you’ve counted the store so that it is months or even a year before you notice the missing merchandise.
Consider instituting surprise audits to reduce the chances that employees will time their theft to your inventory count cycle. If counting the entire inventory on random days isn’t feasible, count the stock on particular shelves, part of the back room, or all of one type of item, for example all of the sweaters, to get an idea of your overall shrinkage due to theft.
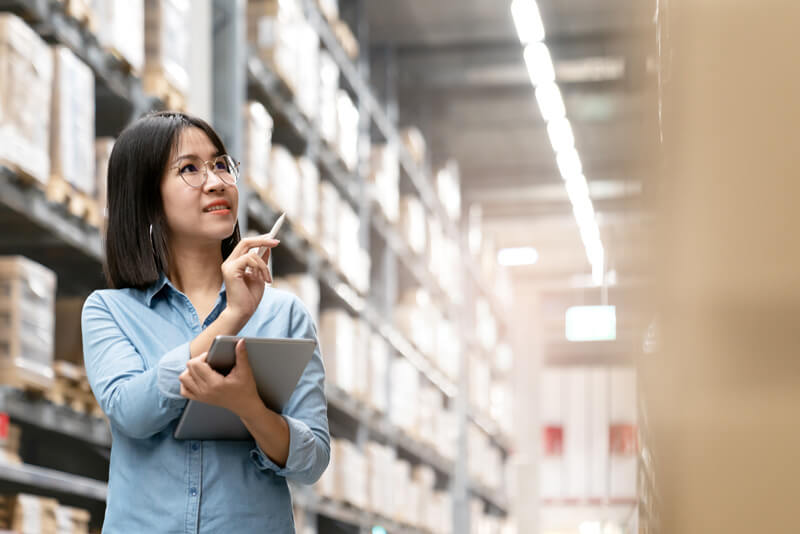
Remote video monitoring
If your inventory shrinkage is rising, it might be time to implement heightened security measures. Solink’s remote video monitoring allows loss prevention managers to see what is happening in hundreds of stores everyday.
Expanding the use of a company like Solink’s remote video monitoring system can provide a more comprehensive overview of daily operations across multiple locations. This advanced technology not only enables loss prevention managers to monitor activities in real time but also records footage for later review. By analyzing video data, managers can identify patterns that may indicate theft or procedural lapses, allowing for targeted improvements in security protocols and operational efficiency.
The buddy system
Whenever possible, there should be two employees working near each other. It’s far less likely that two employees will steal than only one. However, this is only one of the ways that having employees work together can reduce inventory shrinkage.
There are key points at which inventory should be checked. These checks help narrow down when shrinkage has occurred. For example, when an order is received, the manifest should be checked to confirm that all items that were ordered arrived in the store.
This is a good place to institute the buddy system. By having two people check each item on the manifest, you can ensure that any item marked as received has indeed been received.
Educate employees
Ongoing training that details how inventory shrink occurs and why it is important can help you reduce your shrinkage. The important word here is “ongoing” because any effective shrinkage training should be an ongoing discussion with employees.
Inventory shrinkage FAQ
How does inventory shrinkage impact financial reporting and tax obligations for businesses?
Inventory shrinkage can significantly affect a business’s financial statements, distorting financial performance, profitability, and asset valuation. It impacts the balance sheet by reducing inventory value, thus lowering total assets and equity. This can affect financial ratios, such as the current ratio and return on assets, potentially impacting creditworthiness and valuation.
On the income statement, inventory shrinkage can inflate the cost of goods sold (COGS), reducing gross profit and net income, which may erode investor confidence.
It also affects the statement of cash flows by reducing cash flow from operations. To mitigate these effects, businesses should implement robust inventory control measures.
Can implementing a robust return policy help in reducing inventory shrinkage, and if so, how?
It is well-understood in retail management that a robust return policy can help in reducing inventory shrinkage by deterring fraudulent returns and helping manage the return process more efficiently. Effective return policies can also improve inventory accuracy and reduce losses due to theft or fraud, indirectly contributing to shrinkage reduction. Implementing strict return procedures, such as requiring receipts and setting return windows, can help verify the legitimacy of returns and prevent loss.
What are the latest technological advancements in inventory management systems that help prevent shrinkage?
The latest technological advancements in inventory management systems that help prevent shrinkage include automated inventory tracking, real-time analytics, RFID technology, and integrated video security.
These technologies enable businesses to monitor inventory levels accurately, track movements of goods within and outside the store, and identify discrepancies quickly. Automated systems reduce human error, while real-time analytics help in making informed decisions to prevent shrinkage. RFID tags and integrated video security enhance security and reduce theft, one of the primary causes of inventory shrinkage.
Solink inventory shrinkage case study: what happened to the missing box?
12:00: A customer brings a shirt to an associate and asks if they have it in a medium in the back room.
12:15: The associate helped unload the order yesterday and remembers there being a box of shirts. However, they don’t see the box where they placed it the day before. They ask the manager if they know whether someone has moved it.
12:30: The manager opens up Solink on her laptop and performs a motion search where the box of shirts should be. Solink only shows the manager the moments with activity, so it takes only a few minutes to see what happened.
12:32: The manager quickly finds the moment when the box was moved. She sees an employee picking up the box.
12:33: Using Camera Linking, the manager follows the employee on camera as they move through the back room and out the backdoor with the box. Camera Linking automatically maps the overlap of the camera views on a digital floor plan using machine learning so there’s no need to be familiar with the camera names or remember which camera can see what angle.
12:34: The manager saves the clip of the employee taking the box of merchandise and sends it to the loss prevention team at the corporate head office.
To see how Solink can reduce inventory shrinkage across your enterprise, sign up for a demo today.