Table of Contents
Table of Contents
Key performance indicators (KPIs) are essential tools for a warehouse manager, providing crucial insights into the efficiency and effectiveness of warehouse operations. This article explores the various KPIs that warehouse managers should monitor to gauge their performance and ensure optimal functioning of warehouse activities. By understanding and tracking these metrics, warehouse managers can make informed decisions to improve processes, enhance productivity, and drive success in their warehousing strategies.
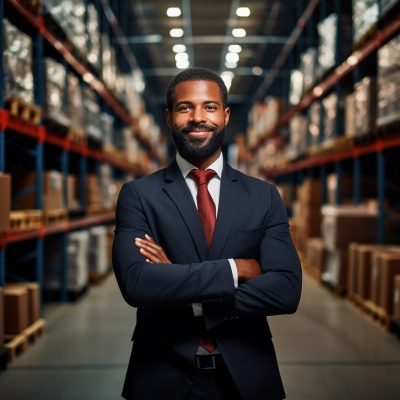
What do warehouse managers do?
Warehouse managers play a crucial role in the smooth operation of warehouses, overseeing various aspects of warehouse management to ensure efficiency, safety, and profitability. Their responsibilities span a wide range of activities, from inventory management to staff supervision, each critical to the success of the warehouse’s operations. By understanding the diverse tasks a warehouse manager handles, one can appreciate the complexity of their role and the importance of using KPIs to track their performance.
One of the primary responsibilities of warehouse managers is to oversee inventory control. This involves ensuring that inventory levels are adequately maintained to meet customer demand without leading to overstocking or stockouts. They are responsible for implementing effective inventory management strategies, which can be assessed using KPIs such as inventory turnover, stockout rate, and inventory accuracy rate. These metrics help in evaluating how well the warehouse manager is balancing inventory supply with demand, managing stock levels, and preventing losses due to shrinkage or excess inventory.
In addition to inventory management, warehouse managers are also tasked with optimizing operational efficiency and managing costs. This includes streamlining processes like order fulfillment, picking and packing, and shipping. KPIs such as order fulfillment cycle time, picking accuracy, and dock-to-stock time are essential for gauging the efficiency of these operations. Cost management is another critical area, with KPIs like warehouse operating expenses, energy cost per square foot, and carrying cost of inventory providing insights into the manager’s ability to control and reduce operational costs. Furthermore, ensuring safety and compliance within the warehouse is paramount, with safety incident rates and compliance audit scores being key indicators of performance in these areas.
Warehouse managers, therefore, need to exhibit a blend of strategic planning, operational oversight, and team leadership. The diverse range of KPIs relevant to their role reflects the multifaceted nature of warehouse management, where success is measured not just in terms of operational efficiency and cost management, but also in maintaining high standards of safety, compliance, and customer satisfaction. Tracking these KPIs is crucial for warehouse managers to identify areas for improvement, make informed decisions, and ultimately drive the warehouse towards greater efficiency and effectiveness.
Essential KPIs for warehouse managers
For warehouse managers, effectively tracking key performance indicators (KPIs) is fundamental to managing and improving warehouse operations. These KPIs provide valuable insights into various aspects of warehouse management, from inventory control and operational efficiency to cost management and customer satisfaction.Â
By closely monitoring these metrics, warehouse managers can identify areas for improvement, optimize processes, and enhance overall performance. This section covers essential KPIs for warehouse managers, including customer satisfaction and service, operational efficiency, cost management, inventory control, and safety and compliance.
Customer satisfaction and service KPIs for a warehouse manager
In warehouse management, customer satisfaction and service are paramount indicators of a warehouse manager’s performance. These KPIs reveal how effectively a manager meets customer expectations and maintains service quality. They are essential because they directly relate to customer retention, brand reputation, and overall business success. High scores in these areas often reflect well on the operational aspects managed by the warehouse manager, from order processing to delivery. Conversely, lower scores can indicate areas needing improvement, such as efficiency in order fulfillment or accuracy in order picking.
Customer complaints and returns
Customer complaints and returns formula: Number of customer complaints and returns/Total number of orders
This KPI tracks the number of customer complaints and returns relative to total orders, indicating customer satisfaction with product quality and service. A lower number is preferable, as it suggests higher customer satisfaction. It’s important to track this metric because it directly reflects on the customer’s experience with your warehouse. High numbers can point to issues in product quality, order accuracy, or customer service.
How to improve customer complaints and returns:
- Enhance quality control measures to reduce product defects.
- Improve order accuracy to ensure correct items are shipped.
- Strengthen customer service support to address issues promptly.
- Gather and analyze feedback to identify common complaint reasons.
- Implement thorough staff training focusing on customer satisfaction.
- Review and optimize return processes for efficiency.
- Monitor and address recurring issues promptly.
Customer satisfaction score
Customer satisfaction score formula: (Total customer satisfaction points/Total number of responses) x 100
This KPI measures the overall customer satisfaction level based on feedback and scores provided by customers. Higher scores indicate better customer satisfaction. Tracking this metric is crucial as it provides direct insight into how customers perceive the quality of service and products. Poor values might suggest problems in various areas like product quality, delivery times, or customer service.
How to improve customer satisfaction score:
- Regularly collect and analyze customer feedback.
- Personalize customer interactions to enhance service quality.
- Implement improvements based on customer suggestions.
- Train staff in customer service excellence.
- Ensure timely and accurate order fulfillment.
- Address and resolve customer issues swiftly and effectively.
- Continuously review and improve customer service policies and practices.
On-time delivery rate
On-time delivery rate formula: (Number of orders delivered on or before the promised date/Total number of orders) x 100
This KPI measures the percentage of orders that are delivered on or before the promised delivery date. Higher percentages are better, indicating reliability and efficiency in fulfilling orders. It’s vital to track this metric as it impacts customer trust and satisfaction. A low on-time delivery rate can lead to customer dissatisfaction and harm the business’s reputation.
How to improve on-time delivery rate:
- Streamline the order processing and fulfillment workflow.
- Use heat maps to understand the flow of inventory through your warehouse.
- Strengthen coordination with shipping and logistics providers.
- Implement real-time tracking for better order management.
- Optimize inventory levels to prevent stockouts.
- Train staff to prioritize and handle orders efficiently.
- Regularly review and adjust delivery schedules.
- Adopt technology solutions for efficient route planning.
Operational efficiency KPIs for a warehouse manager
Operational efficiency KPIs are critical for evaluating how effectively and efficiently a warehouse manager oversees the warehouse’s day-to-day operations. These metrics give insights into the manager’s ability to optimize processes, manage resources, and maintain productivity. High performance in these areas often translates to lower operational costs, quicker turnaround times, and increased overall throughput. On the other hand, lower scores in operational efficiency can indicate areas needing improvement, such as workflow optimization, labor management, or process automation.
Dock-to-stock time
Dock-to-stock time formula: Total time taken to move goods from receiving dock to storage/Total number of items received
This KPI measures the time taken to move goods from the receiving dock to storage, reflecting the efficiency of the receiving process. Shorter times are better, indicating swift and efficient handling. It’s important to track this metric as it affects the overall turnaround time of inventory and readiness for order fulfillment. Lengthy dock-to-stock times can indicate inefficiencies in unloading, inspection, or warehousing.
How to improve dock-to-stock time:
- Streamline the receiving and inspection process.
- Implement automated systems for quick sorting and movement.
- Train staff on efficient unloading and storing techniques.
- Optimize warehouse layout for faster movement of goods.
- Schedule and manage incoming shipments to prevent congestion.
- Regularly review and adjust handling procedures.
- Utilize technology for inventory tracking and management.
Inventory turnover
Inventory turnover formula: Cost of goods sold/Average inventory value
This KPI indicates how often inventory is sold and replaced over a specific period, reflecting inventory management effectiveness. Higher turnover rates are better, suggesting efficient inventory usage and sales. Tracking this metric is crucial for understanding product demand and stocking efficiency. Low inventory turnover might suggest overstocking, slow-moving items, or suboptimal sales performance.
How to improve inventory turnover:
- Align inventory with market demand through accurate forecasting.
- Implement effective pricing and promotional strategies.
- Optimize the product mix based on sales trends and customer preferences.
- Improve supplier relations for quicker inventory replenishment.
- Regularly review and adjust inventory levels.
- Train staff in inventory management best practices.
- Analyze sales data to identify and address slow-moving items.
Labor utilization rate
Labor utilization rate formula: (Total productive labor hours/Total available labor hours) x 100
This KPI measures the percentage of labor capacity that is effectively utilized in the warehouse. Higher rates indicate better use of the workforce and greater labor efficiency. It’s important to track this metric to assess workforce productivity and identify areas for labor optimization. Low labor utilization rates can indicate underutilization of staff, inefficiencies in task allocation, or the need for process improvements.
How to improve labor utilization rate:
- Implement workforce planning and scheduling optimization.
- Train employees to enhance skill sets and versatility.
- Streamline warehouse processes to reduce idle time.
- Adopt technology to automate repetitive tasks.
- Foster a culture of continuous improvement and efficiency.
- Regularly review and realign tasks and responsibilities.
- Implement performance monitoring and incentivization programs.
Order fulfillment cycle time
Order fulfillment cycle time formula: Total time taken from receiving an order to its fulfillment/Total number of orders
This KPI measures the time taken from the receipt of an order to its fulfillment, indicating the efficiency of the order processing system. Shorter cycle times are preferable, as they reflect quicker order processing and delivery. Tracking this metric is vital for assessing the warehouse’s responsiveness to customer orders. Extended fulfillment times can suggest bottlenecks in picking, packing, or shipping processes.
How to improve order fulfillment cycle time:
- Optimize inventory levels for faster order processing.
- Streamline picking and packing processes.
- Implement efficient order management systems.
- Enhance collaboration with shipping partners for quicker dispatch.
- Train staff for efficient handling of orders.
- Regularly review and refine the entire order processing workflow.
- Utilize technology for real-time order tracking and management.
Picking accuracy
Picking accuracy formula: (Total correct picks/Total picks) x 100
This KPI assesses the accuracy in selecting the correct items for orders, crucial for order fulfillment quality. Higher accuracy rates are better, indicating fewer errors in the picking process. It’s essential to track this metric as it impacts customer satisfaction and order reprocessing costs. Low picking accuracy can lead to increased returns, customer dissatisfaction, and additional costs for correcting errors.
How to improve picking accuracy:
- Implement barcode scanning or RFID technology for accurate picking.
- Train staff on proper picking techniques and accuracy.
- Use pick-to-light systems or other visual aids for error reduction.
- Regularly conduct quality checks and audits.
- Organize inventory strategically to minimize picking errors.
- Encourage a focus on accuracy among the workforce.
- Review and refine picking routes and strategies.
Cost management KPIs for a warehouse manager
Cost management KPIs are essential for warehouse managers to track and control the various costs associated with warehouse operations. These KPIs provide insights into how effectively a manager is optimizing resources, reducing unnecessary expenses, and maintaining profitability. Effective cost management directly impacts the bottom line and can lead to significant savings. Poor performance in this area can indicate areas where costs can be reduced, such as in inventory holding, energy usage, or operational inefficiencies.
Carrying cost of inventory
Carrying cost of inventory formula: (Total inventory holding costs/Average inventory value) x 100
This KPI measures the total cost associated with storing unsold goods, including expenses like warehousing, insurance, and depreciation. Lower values are preferable, indicating efficient inventory management and reduced holding costs. Tracking this metric is important to understand the financial impact of inventory storage and to identify areas where cost savings can be made. High carrying costs might suggest overstocking, inefficient storage, or opportunities for better inventory turnover.
How to improve carrying cost of inventory:
- Optimize inventory levels to reduce excess stock.
- Enhance inventory turnover through effective demand forecasting.
- Implement just-in-time inventory strategies.
- Negotiate better rates with storage and insurance providers.
- Improve warehouse layout for efficient space utilization.
- Regularly review and adjust safety stock levels.
- Utilize efficient inventory management software.
Cost per unit shipped
Cost per unit shipped formula: Total shipping cost/Number of units shipped
This KPI calculates the average cost involved in shipping each unit, reflecting the efficiency of the shipping process. Lower costs per unit are better, indicating cost-effective shipping practices. It’s crucial to track this metric to manage shipping costs effectively and maintain profitability. High costs per unit can signal inefficiencies in the shipping process, overpriced carrier services, or opportunities for optimization.
How to improve cost per unit shipped:
- Negotiate better rates with shipping carriers.
- Optimize packaging to reduce weight and size.
- Consolidate shipments to maximize efficiency.
- Implement route optimization for deliveries.
- Streamline order consolidation and handling processes.
- Regularly review and compare carrier performance and rates.
- Adopt bulk shipping strategies where applicable.
Energy cost per square foot
Energy cost per square foot formula: Total energy costs/Total warehouse area
This KPI measures the energy efficiency of the warehouse, indicating the cost of energy relative to the size of the facility. Lower values are preferable, suggesting more efficient energy usage. Monitoring this metric is key for identifying opportunities to reduce energy costs and enhance sustainability. High energy costs per square foot can indicate inefficient lighting, heating, or cooling systems, or poor insulation.
How to improve energy cost per square foot:
- Upgrade to energy-efficient lighting and HVAC systems.
- Implement energy management and monitoring systems.
- Insulate the warehouse to maintain optimal temperatures.
- Utilize natural lighting where possible.
- Schedule regular maintenance for energy systems.
- Train staff in energy conservation practices.
- Optimize equipment and machinery usage for energy efficiency.
Return processing costs
Return processing costs formula: Total costs associated with processing returns/Total number of returns
This KPI tracks the cost involved in handling and processing returned items, reflecting the efficiency of the return process. Lower costs are better, indicating a more efficient and cost-effective return process. It’s important to monitor this metric to manage return costs and improve reverse logistics. High return processing costs can suggest inefficiencies in handling, restocking, or waste in the returns process.
How to improve return processing costs:
- Streamline the return process with clear guidelines and procedures.
- Implement efficient systems for tracking and processing returns.
- Train staff on quick and effective handling of returns.
- Optimize restocking or disposal of returned items.
- Regularly review and refine return policies and processes.
- Minimize return rates through quality control and accurate order fulfillment.
- Use technology for automated return processing.
- Investigate the potential of internal theft.
Warehouse operating expenses
Warehouse operating expenses formula: Total expenses incurred in warehouse operations/Total number of orders processed
This KPI measures the overall cost of running the warehouse, including labor, utilities, maintenance, and other operational expenses. Lower expenses are preferable, indicating efficient and cost-effective warehouse management. Tracking this metric is crucial for identifying areas where operational costs can be optimized. High warehouse operating expenses can point to inefficiencies in resource utilization, opportunities for cost savings, or areas needing process improvements.
How to improve warehouse operating expenses:
- Optimize labor scheduling and utilization to reduce costs.
- Implement energy-saving measures and equipment.
- Conduct regular maintenance to prevent costly repairs.
- Streamline operational processes for efficiency.
- Negotiate better rates with suppliers and service providers.
- Utilize technology for automated and efficient operations.
- Regularly audit expenses to identify and address cost drivers.
Inventory control KPIs for a warehouse manager
Inventory control KPIs are crucial for warehouse managers to ensure optimal inventory levels, minimize stockouts, and maintain accurate inventory records. These metrics help in assessing how well a warehouse manager is balancing inventory supply with demand, managing stock levels, and preventing losses due to shrinkage or excess inventory. Effective inventory control is key to reducing holding costs, improving order fulfillment, and maintaining customer satisfaction. Poor performance in these KPIs can indicate issues such as overstocking, understocking, or inefficiencies in inventory management practices.
Backorder rate
Backorder rate formula: (Number of items backordered/Total number of items ordered) x 100
This KPI measures the rate at which items ordered are not immediately available from stock and need to be backordered. A lower rate is preferable, indicating better stock availability and fulfillment capabilities. It’s important to monitor this metric as high backorder rates can lead to customer dissatisfaction and potential loss of sales. This metric helps assess inventory planning and forecasting effectiveness.
How to improve backorder rate:
- Enhance demand forecasting to align inventory with customer needs.
- Maintain optimal inventory levels to prevent stockouts.
- Strengthen supplier relationships for timely inventory replenishment.
- Implement just-in-time inventory practices.
- Regularly review and adjust safety stock levels.
- Analyze and address frequent causes of backorders.
- Utilize advanced inventory management systems for real-time tracking.
Excess inventory percentage
Excess inventory percentage formula: (Amount of excess inventory/Total inventory) x 100
This KPI indicates the proportion of inventory that exceeds the normal requirement, highlighting overstocking issues. Lower percentages are better, as they suggest a more balanced inventory level. Tracking this metric is crucial for avoiding the costs associated with excess inventory, such as increased storage and potential obsolescence. High excess inventory percentages can signal issues in demand forecasting or inventory management.
How to improve excess inventory percentage:
- Implement more accurate demand forecasting techniques.
- Regularly review and adjust inventory levels.
- Adopt lean inventory management practices.
- Dispose of or discount slow-moving or obsolete stock.
- Enhance supplier relationships for flexible inventory handling.
- Train staff in effective inventory management techniques.
- Use inventory management software for better control and visibility.
Inventory accuracy rate
Inventory accuracy rate formula: (Number of accurate inventory records/Total inventory records) x 100
This KPI measures the accuracy of inventory records in comparison to the actual stock on hand. Higher rates indicate better inventory record accuracy, crucial for efficient operations. Accurate inventory records are vital for effective order fulfillment, planning, and decision-making. Low accuracy rates can lead to issues like stockouts, overstocking, and poor customer service.
How to improve inventory accuracy rate:
- Conduct regular inventory audits and reconciliations.
- Implement robust inventory management systems.
- Utilize barcode or RFID technology for accurate tracking.
- Train staff on proper inventory recording and handling procedures.
- Foster a culture of accountability and attention to detail.
- Regularly review and update inventory counting and recording practices.
- Address discrepancies promptly to maintain accurate records.
Shrinkage rate
Shrinkage rate formula: (Total recorded inventory – Physical inventory count)/Total recorded inventory x 100
This KPI measures the percentage of inventory loss due to factors such as theft, damage, or administrative errors. Lower shrinkage rates are preferable, indicating better control over inventory and reduced losses. It’s essential to track this metric to identify and address the causes of inventory shrinkage. High shrinkage rates can significantly impact profitability and indicate issues in security, handling, or inventory management.
How to improve shrinkage rate:
- Enhance security measures and video monitoring within the warehouse.
- Conduct regular inventory audits to detect and address shrinkage.
- Implement strict procedures for inventory handling and storage.
- Use technology for accurate inventory tracking and management.
- Train staff on inventory protection and loss prevention practices.
- Investigate and resolve discrepancies promptly.
- Address operational inefficiencies leading to damage or loss.
Stockout rate
Stockout rate formula: (Number of stockouts/Total inventory items) x 100
This KPI measures the frequency at which items in inventory are out of stock and unavailable for immediate order fulfillment. Lower rates are better, as they indicate effective inventory management and consistent product availability. Monitoring this metric is key for ensuring that customer demand is met and for minimizing lost sales opportunities and others forms of operational shrinkage. Frequent stockouts can lead to customer dissatisfaction and harm the business’s reputation.
How to improve stockout rate:
- Implement accurate demand forecasting to anticipate inventory needs.
- Maintain optimal inventory levels to meet customer demand.
- Enhance supplier relationships for timely inventory replenishment.
- Utilize just-in-time inventory practices to manage stock levels.
- Regularly review safety stock levels and adjust as needed.
- Train staff in effective inventory management and forecasting.
- Adopt advanced inventory management systems for real-time monitoring.
Safety and compliance KPIs for a warehouse manager
Safety and compliance KPIs are vital for warehouse managers to ensure a secure working environment and adherence to regulatory standards. These metrics assess a manager’s effectiveness in maintaining safety protocols, preventing accidents, and complying with industry regulations. Strong performance in these areas is crucial for protecting employees, avoiding legal issues, and ensuring uninterrupted operations. Poor scores may indicate potential safety hazards, insufficient training, or non-compliance issues, all of which can have serious implications for the warehouse.
Compliance audit scores
Compliance audit scores formula: (Total points achieved in compliance audit/Total possible points) x 100
This KPI measures the warehouse’s adherence to industry standards and regulatory requirements, as evaluated during compliance audits. Higher scores are preferable, indicating better compliance and adherence to standards. Monitoring this metric is essential for ensuring that the warehouse operates within legal and regulatory frameworks. Low scores can lead to legal repercussions, penalties, and damage to the warehouse’s reputation.
How to improve compliance audit scores:
- Regularly review and update compliance policies and procedures.
- Conduct internal audits to prepare for external evaluations.
- Train staff on compliance standards and practices.
- Implement systems and processes that ensure regulatory adherence.
- Stay updated on industry regulations and standards.
- Foster a culture of compliance and ethical practices.
- Engage with compliance experts or consultants for guidance.
Safety incident rate
Safety incident rate formula: (Number of safety incidents/Total hours worked) x 1,000
This KPI tracks the frequency of safety-related incidents, such as accidents or injuries, in the warehouse. Lower rates indicate a safer work environment and effective safety measures. It’s crucial to monitor this metric to proactively manage warehouse safety and reduce the risk of accidents. High safety incident rates can result in employee harm, operational disruptions, and potential legal issues.
How to improve safety incident rate:
- Implement comprehensive safety training for all employees.
- Regularly conduct safety drills and awareness sessions.
- Ensure proper maintenance and safety checks of equipment.
- Use cloud-based security cameras to monitor for safety risks.
- Foster a workplace culture that prioritizes safety.
- Encourage reporting and prompt addressing of safety hazards.
- Regularly review and update safety protocols and equipment.
- Involve employees in safety committees and improvement initiatives.
Use Solink to track KPIs for warehouse managers
Solink provides an innovative solution for tracking the performance of warehouse managers through its cloud-based video security and analytics platform. This tool enables the monitoring of crucial KPIs, offering insights into various aspects of warehouse management.Â
From inventory control to operational efficiency, Solink’s integration of video data with transactional data delivers a comprehensive view, aiding warehouse managers in optimizing processes and ensuring effective oversight. By utilizing Solink, businesses can enhance decision-making, streamline operations, and elevate the overall performance of their warehouse management.
To see how Solink can improve your warehouse manager’s job performance, sign up for a demo today.